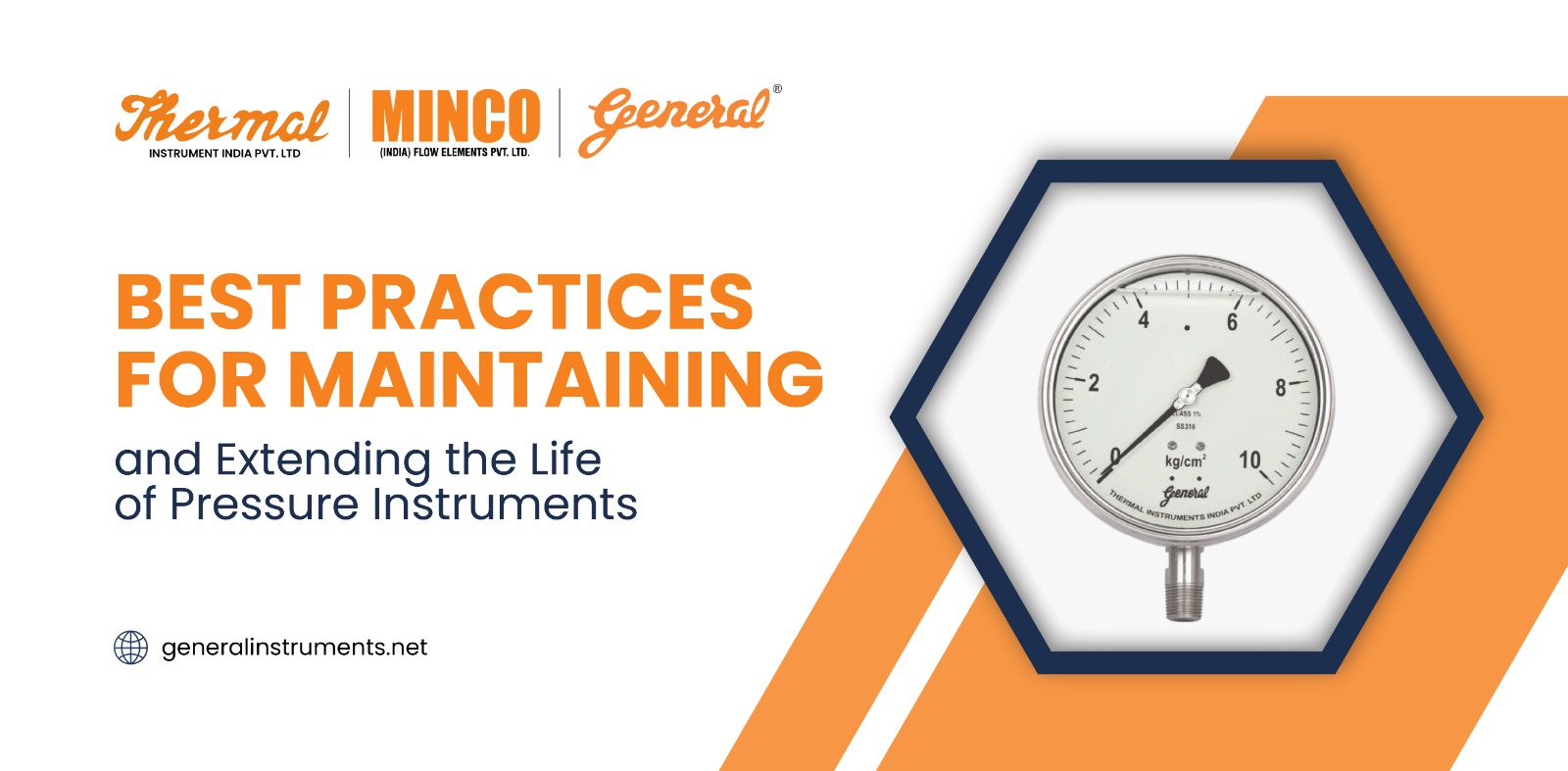
Best Practices for Maintaining and Extending the Life of Pressure Instruments
Pressure gauges, being essential elements of diverse processing systems, have the challenge of requiring dependability, precision, and legibility. Their function is critical in preventing operational breakdowns that occur during routine industrial operations.
As a result, the construction and testing methodologies employed in the manufacture of pressure gauges assume critical importance, as they significantly impact their dependability, safety, and ability to provide peace of mind. Within an industrial environment characterised by significant financial, time, and productivity setbacks, failings carry unquestionably high stakes.
This blog aims to lay out the most important information on Best Practices for Maintaining and Extending the Life of Pressure Instruments.
Importance of Maintenance:
Performing routine maintenance on your vehicle is equivalent to caring for it so that it operates efficiently. Additionally, pressure instruments must be utilised with care to function properly. Regular maintenance of the instruments ensures their optimal condition, avoids potential issues, and extends their operational lifespan. Early identification and resolution of issues are like performing a comprehensive examination.
Pressure measurement devices assist in maintaining constant and consistent pressure levels. Consequently, these instruments ensure the efficient operation of machinery. This increases process efficacy and decreases production downtime. Utilising these devices boosts productivity and enhances plant operations.
Significance of Cleaning and Inspection:
If you compare pressure instruments to windows, you’ll understand why they must be kept clean. It’s like bathing pressure instruments and looking to see if they have any scratches or cracks. Keeping them clean makes sure that the numbers are correct, and finding any damage early on helps stop problems from getting worse.
Methods for Extending the Life of Pressure Instruments:
Consider your pressure instrument to be an exceptional being whose abilities are the processes that allow it to remain effective and robust.
- Calibration: Pressure instrument calibration frequency varies on instrument type, usage frequency, and surrounding conditions. Calibrating every six to twelve months is recommended. More critical applications may need calibration every three to six months. Regular calibration assures precise pressure readings, improving process efficiency.
- Zero-Point Adjustment: The design, usage, and precision of pressure instruments determine their zero-point adjustment frequency. Monthly or quarterly zero-point adjustment is advised. When operating conditions change or the instruments are heavily used, bi-weekly or monthly adjustments may be needed. Regular zero-point adjustments ensure the instrument’s reliability by maintaining precise readings without pressure.
- Seals, the Protectors: Pressure instrument seal replacement frequency varies on seal type, climatic conditions, and wear and tear. Seals should be inspected and assessed regularly, usually at three-month to one-year maintenance periods. If inspections reveal wear, damage, or degeneration, replacement is necessary. For seal integrity and effectiveness, the pressure instrument may need more frequent checks and replacements if it is used frequently or in harsh environments.
- Installations: Correctly installing pressure instruments is equivalent to constructing a home upon a sturdy foundation. If you adhere to the manufacturer’s instructions, the environment in which your instrument is stored will be secure and stable.
- Temperature Considerations: Extreme temperatures are harmful to pressure instruments; transporting them to the North Pole or a desert is equivalent to damaging them. Select instruments that are resistant to the working environment’s temperature. Similar to providing them with appropriate attire to ensure their comfort.
- Regular Check-ups: Imagine if doctors only saw people with serious illnesses. Like frequent medical exams, pressure instrument inspections are essential for health. These check-ups are usually done monthly to quarterly, depending on usage and climate. During these examinations, look for wear, damage, or departures from typical operating norms. This proactive technique detects issues early, preserving pressure instrument health.
In conclusion, maintaining pressure instruments is similar to caring for a companion in that you desire their optimal condition and longevity. Adhering to these uncomplicated procedures not only guarantees the precision of your pressure instruments but also extends their lifespan, thereby facilitating the operation of your processes with maximum efficiency.